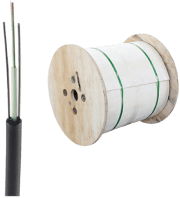
RECOIN CABLE
Short description:
PRODUCT DESCRIPTION
TECHNICAL STANDARDS FOR OPTICAL CABLES
General introduction:
- Recoin's metallic and non-metallic fiber optic cables use single-mode optical fiber, placed in a loose tube filled with specialized moisture-proof oil, with a moisture barrier, a protective cover for non-metallic cables and two layers. Protective cover for metal cables and hanging wires made of galvanized braided steel. Fiber capacity from 2 to 144 fibers.
- Recoin's cables are fully compliant with popular international standards IEC, EIA, ASTM, national standards TCVN, TCN industry standards or customer standards...
Product symbol
– Cable car without steel tape: TPKL 2C – 144C
– Cable car with steel tape: TKL 2C – 144C
– Cable car with steel tape: TKL 2C – 144C
Simulation of suspended fiber optic cable structure without steel tape (TPKL)


Technical characteristics of single-mode fiber G 652D

Detailed components of the cable
The optical fiber used is single-mode fiber G.652D, step refractive index.
The outside of the optical fiber is color-coated (coded) according to TIA/EIA - 598 - A standards.
The primary shell as well as the color ink covering the optical fiber use a material that resists the effects of ultraviolet rays (acrylate), minimizing the impact of the external environment and being durable over time.
When welding, the primary shell is easily stripped using specialized equipment, does not require the use of chemicals and does not affect the fibers.
Components of optical fiber such as core, shell, ink... do not conduct electricity.
The standard parameters of optical fibers are specified in the table above.
All the fiber optics used in a cable come from a single fiber optic manufacturer.
The color coding law of optical fibers in the same liquid buffer tube is specified according to the following table:
The outside of the optical fiber is color-coated (coded) according to TIA/EIA - 598 - A standards.
The primary shell as well as the color ink covering the optical fiber use a material that resists the effects of ultraviolet rays (acrylate), minimizing the impact of the external environment and being durable over time.
When welding, the primary shell is easily stripped using specialized equipment, does not require the use of chemicals and does not affect the fibers.
Components of optical fiber such as core, shell, ink... do not conduct electricity.
The standard parameters of optical fibers are specified in the table above.
All the fiber optics used in a cable come from a single fiber optic manufacturer.
The color coding law of optical fibers in the same liquid buffer tube is specified according to the following table:
FIBER_TYPE | SINGLE_MODE_G652D |
MODE_FIELD_DIAMETER | DIAMETER_AT_1310NM
DIAMETER_AT_1550NM WAVELENGTH_1310_TOLERANCE WAVELENGTH_1550_TOLERANCE |
CLADDING_DIAMETER_TOLERANCE | CLADDING_DIAMETER_VALUE |
CORE_CONCENTRICITY_ERROR | CORE_CONCENTRICITY_ERROR_VALUE |
CLADDING_NON_CIRCULARITY | CLADDING_NON_CIRCULARITY_VALUE |
OUTER_COATING_DIAMETER | OUTER_COATING_DIAMETER_VALUE |
CUTOFF_WAVELENGTH | CUTOFF_WAVELENGTH_VALUE |
ATTENUATION_COEFFICIENT | ATTENUATION_1310NM_MAX
ATTENUATION_1310NM_AVG
ATTENUATION_1550NM_MAX
ATTENUATION_1550NM_AVG ATTENUATION_1310NM_DETAILS ATTENUATION_1550NM_DETAILS |
DISPERSION_COEFFICIENT | DISPERSION_1310NM
DISPERSION_1550NM DISPERSION_DETAILS |
ZERO_DISPERSION_WAVELENGTH | ZERO_DISPERSION_WAVELENGTH_VALUE |
ZERO_DISPERSION_SLOPE | ZERO_DISPERSION_SLOPE_VALUE |
PMD_COEFFICIENT | PMD_COEFFICIENT_VALUE |
Made from non-metallic material FRP (Fiber Reinforce Platic) with uniform circular structure/dimensions, continuous, non-conductive, unconnected throughout the entire length of the cable roll, without any defects. You can cover the cable with PE plastic if necessary to create an even roundness for the cable.
This component helps prevent the cable and optical fiber from being too stretched and still ensures the cable's flexibility throughout the process from production, transportation, installation, and use.
This component helps prevent the cable and optical fiber from being too stretched and still ensures the cable's flexibility throughout the process from production, transportation, installation, and use.
Loose tubes are manufactured from Polybutylene Terephthalate (PBT) material, which is non-conductive. Loose tubes in a cable are color coded according to EIA/TIA-598 standards and are specified as in the table below.
This loose tube contains optical fibers inside and is filled with specialized moisture-proof oil (filler). The optical fibers are free and move easily.
The diameter of the loose tube depends on the number of optical fibers in the tube
The number of optical fibers in each loose tube is specified as follows:
– 6 fibers/loose tube for ${"< ="} 30 fiber cable,:
– 12 optical fibers/loose tube for cables with 36 fibers or more.
This loose tube contains optical fibers inside and is filled with specialized moisture-proof oil (filler). The optical fibers are free and move easily.
The diameter of the loose tube depends on the number of optical fibers in the tube
The number of optical fibers in each loose tube is specified as follows:
– 6 fibers/loose tube for ${"< ="} 30 fiber cable,:
– 12 optical fibers/loose tube for cables with 36 fibers or more.
In case to form an evenly round cable core with a solid structure but the number of loose tubes is not enough to create an even roundness for the cable, use an additional filler rod (Filler Rod).
This auxiliary buffer tube is made from Polyethylene (PE) plastic with a natural color that does not match the color of any liquid tube and these tubes do not contain optical fibers or any metal components, and are not electrically conductive.
This auxiliary buffer tube is made from Polyethylene (PE) plastic with a natural color that does not match the color of any liquid tube and these tubes do not contain optical fibers or any metal components, and are not electrically conductive.
The spaces between the fiber and the inner surface of the liquid tube lumen are filled with a special compound (Thixotropic Jelly Compound). This compound has the effect of preventing water and moisture penetration into the tube, helping to ensure stable transmission quality.
This filler is not toxic to human health, does not affect other components in the cable as well as the color of the optical fiber. This substance is colorless, odorless, does not mold, and does not conduct electricity.
This filler is non-conductive and has a low coefficient of thermal expansion, ensuring it does not harden at very low temperatures. Does not hinder the movement of fibers in loose tubes.
This filler is not toxic to human health, does not affect other components in the cable as well as the color of the optical fiber. This substance is colorless, odorless, does not mold, and does not conduct electricity.
This filler is non-conductive and has a low coefficient of thermal expansion, ensuring it does not harden at very low temperatures. Does not hinder the movement of fibers in loose tubes.
The cable core is waterproofed and moisture-proof using the dry cable core method (quick desiccant compound - SAP), this compound completely protects the cable core from water as well as moisture from penetrating the cable, ensuring Cable cores are always dry in all environments. The entire cable core waterproof component includes the following 2 components:
Water swellable tape is wound along the entire outside and along the length of the cable core and water swellable yarn is wound around the central load-bearing member and continuously throughout the length of the cable.
These two components ensure absolute prevention of water and moisture penetration into the cable core, tape and waterproof fiber. These waterproof fibers are non-conductive, insulating, non-flammable and anti-mold.
Water swellable tape is wound along the entire outside and along the length of the cable core and water swellable yarn is wound around the central load-bearing member and continuously throughout the length of the cable.
These two components ensure absolute prevention of water and moisture penetration into the cable core, tape and waterproof fiber. These waterproof fibers are non-conductive, insulating, non-flammable and anti-mold.
The loose tubes are arranged sequentially along with other components such as auxiliary buffer tubes (filler tubes) if necessary and are twisted SZ in reverse along the axis of the central load-bearing fiber. The above cable core is wound with two polyester yarn binders in opposite directions, with enough tension to ensure the cable core is sturdy, maintaining the order and position of the cable components throughout the production, construction and use process. use.
The braiding steps and excess fiber in the loose tube ensure that the actual fiber excess in the cable compared to the length printed on the cable is guaranteed to be ≥ 1%.
The braiding steps and excess fiber in the loose tube ensure that the actual fiber excess in the cable compared to the length printed on the cable is guaranteed to be ≥ 1%.
Using many Aramid yarns with very high tension resistance, adding primary reinforcement helps increase the tension resistance of the cable core as well as the cable. These additional reinforcing fibers are placed outside the waterproof tape, arranged evenly and tightly braided to the inner cable core.
Corrugated steel tape protects the cable from mechanical impacts and rodents. The tape is wound along the entire cable core with the overlap of the steel tape being at least 3 mm. The outer diameter of the steel tape overlapping part is equal to the outer diameter of the corrugated part.
This steel tape is made from steel material coated with Ethylene arcylic copolymer on both sides.
This steel tape is made from steel material coated with Ethylene arcylic copolymer on both sides.
It is a high-quality black carbon-containing HDPE plastic layer that can withstand the effects of ultraviolet rays, contains appropriate antioxidants, is not capable of mold growth, and does not contain metal components.
The shell has a uniform thickness, is evenly round over the entire length of the cable, uniform quality, no roughness, no air bubbles, no splits, no cracks, blisters, lumps or any defects. What disability?
Cable sheath thickness: ≥ 1.5mm.
The shell has a uniform thickness, is evenly round over the entire length of the cable, uniform quality, no roughness, no air bubbles, no splits, no cracks, blisters, lumps or any defects. What disability?
Cable sheath thickness: ≥ 1.5mm.
– Use 7/1.0mm hanging wire for cables with a capacity of up to 72 fibers
– Use 7/1.2mm hanging wire for cables with a capacity of 96 fibers or more
– Use 7/1.2mm hanging wire for cables with a capacity of 96 fibers or more